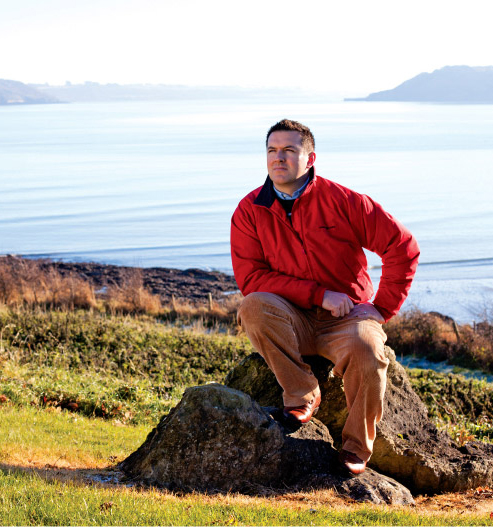
PUTTING PATIENTS FIRST “Close collaboration with colleagues throughout the supply chain allows me to gain a holistic appreciation of the steps between my activities and each patient,” says Ray Hanley in Cork, Ireland. When such insights are used in decision-making, “It’s how we put patients first.”
Pathway to Patients
“There’s a pride and also a big sense of responsibility in what we do,” says Ray Hanley, Operations Development Coordinator, DePuy (Ireland). “Some 600 knees leave here every day to be implanted in patients around the world.”
Johnson & Johnson Supply Chain (JJSC) helps coordinate the path that our health care products take to reach people—doctors, nurses and patients, mothers, fathers and other caregivers—and meet their needs.
“Processing orders, myself and others I work with genuinely feel how important it is to get high-quality product to where it ought to be,” says Elaine Eager, International Supply Group Team Leader, DePuy (Ireland), who once personally transported a knee implant to a hospital due to an urgent patient need. “It’s not simply about moving product from one place to another—it’s about transforming lives.”
Worldwide, JJSC includes a network of manufacturing sites, external manufacturers, distribution centers and approximately 50,000 associates.
“Our supply chain organization is a large part of who we are as a company and plays a vital role in our ability to meet the needs of our customers,” says Ajit Shetty, Ph.D., Corporate Vice President responsible for JJSC. “We have deployed a new supply chain operating model that will enable growth, drive quality and compliance, and help us run more efficiently so we can more effectively serve patients and consumers worldwide.”
A NEW HOLISTIC MODEL
The formation of an enterprise supply chain operating model was announced in January 2010. Objectives of the new organization are to enable growth, drive quality and compliance, improve costs and provide professional development for our people.
Created by business leaders in all three sectors, the model will coordinate essential supply chain functions—like procurement, customer and logistics services, and asset allocation—while maintaining critical decentralization of sector operating companies, one of the proven strategies of Johnson & Johnson.
“Ultimately, this new approach to the supply chain will improve the experience our customers have when doing business with Johnson & Johnson companies while generating incremental value for our businesses,” says Shetty.
ENABLING PERFORMANCE TODAY
The organizational design for JJSC includes a new operating model for Quality & Compliance (Q&C) and a new structure for Supply Chain Strategy and Project Management. Cross-sector collaboration that the new enterprise model helps facilitate is already playing out in recovery plans related to manufacturing issues experienced at McNeil Consumer Healthcare.
“The McNeil situation has all of us rethinking business continuity planning and how we utilize our plants and partner suppliers,” says Robert Salerno, Vice President, Supply Chain Strategy and Project Management, JJSC. “Rather than plan around one operating unit, we can approach manufacturing from a Johnson & Johnson vantage point. With the new supply chain model, we’re more able to leverage assets, best practices, systems and technologies while offering supply chain leaders professional development opportunities across our companies.”
The new operating model will also create a single framework for Q&C across companies, inclusive of common quality standards by product types such as devices, drugs and combination products.
“By standardizing processes in our quality systems and by providing greater oversight in this area, we can reduce complexity and risk in the area of quality,” says Kathy Wengel, Chief Quality Officer, JJSC.
NURTURING GROWTH TOMORROW
In addition to improving quality and compliance, the new model is designed to enable growth and improve efficiency and effectiveness. Again, cross-sector collaboration—key to bringing forth health care technologies that draw on expertise from more than one business segment—will flourish as manufacturing and quality experts from various business units have opportunities to combine their talents.
“Campus Ireland” is one example. There are six manufacturing facilities in Ireland across our Medical Devices and Diagnostics and Pharmaceutical businesses. The close proximity of these facilities enables the companies to work collaboratively on a range of projects while facilitating the transfer of employees between sites for specific projects, career development and promotion opportunities. Campus leaders in Ireland are also working toward creation of a shared state-of-the-art manufacturing facility for convergent medical technology products.
“Our journey to coordinate our supply chain organizations is under way,” Shetty says. “The operating model has the potential to benefit those we serve by driving quality, efficiency and effectiveness in all we do and touching—and transforming—lives for years to come.”